di Giorgio Piazza
In molte applicazioni industriali la misura della pressione, così come quella di altri variabili (temperatura, portata, concentrazioni chimiche e pressione), è indispensabile per tenere sotto controllo l’andamento del processo.
Regolare la pressione può essere un’esigenza utile in molti contesti, per esempio nei sistemi di stoccaggio di sostanze chimiche, per controllare un filtro dell’aria o un ventilatore di un impianto di condizionamento oppure, come vedremo nel dettaglio, per monitorare il funzionamento di una pompa centrifuga.
Nell’industria la misurazione della pressione viene effettuata grazie ai manometri, che rappresentano una soluzione robusta e di facile utilizzo: questi strumenti generalmente contengono un elemento sensibile che si deforma, sollecitato dalla pressione del fluido di processo. Il manometro può essere realizzato in materiale differente: lega di rame, acciaio nelle diverse esecuzioni oppure, nei casi particolari, materiali speciali.
La pressione di processo è misurata in relazione ad una pressione di riferimento che corrisponde alla “pressione atmosferica”: il manometro indica quanto è maggiore o inferiore la pressione misurata rispetto a questo valore.
Negli impianti industriali è possibile prevedere contatti elettrici per l’indicazione della pressione minima o massima, oppure trasmettitori che possono fornire un segnale elettrico proporzionale alla pressione; in casi di vibrazioni o di alti carichi dinamici la cassa degli strumenti può anche essere riempita di liquido.
Esistono diverse tipologie di manometri: possono essere a molla tubolare, a membrana, a capsula e a soffietto e possono essere equipaggiati con accessori elettrici ed elettronici e combinati con separatori di pressione nelle più diverse applicazioni.
-
Separatori e manometri -
Trasmettitori di pressione -
Trasmettitori di pressione compatti
Scelta dello strumento
Veniamo dunque alla scelta dello strumento: nel contesto di ogni applicazione è importante considerare alcune variabili che possono indirizzare alla scelta del corretto strumento:
– pressione d’esercizio e pressione massima;
– range di temperatura;
– natura e stato del fluido di processo;
– presenza di variazioni regolari di pressione (pressione pulsante);
– possibilità di variazioni irregolari e/o accidentali della pressione (pressione pulsante);
– presenza di vibrazioni sull’impianto;
– impiego in ambienti corrosivi;
– temperatura ambiente.
Per garantire la possibilità di effettuare la misurazione efficacemente nelle situazioni più diverse, esistono manometri completamente privi di parti metalliche: per la loro particolare resistenza alla corrosione, questi possono essere impiegati anche in ambienti molto aggressivi. Ci sono varianti che possono essere utilizzate anche in caso di carichi variabili e con forti vibrazioni.
I separatori per manometri
Quando il sensore non può rimanere a contatto con il fluido di misura, si monta sul manometro un separatore di membrana, formato da una membrana flessibile in gomma EPDM con rivestimento in PTFE, che separa il fluido dal manometro.
I separatori sono spesso utilizzati nell’industria chimica, in applicazioni dove sono impiegati liquidi aggressivi, nella depurazione delle acque, dove il fluido movimentato ha notevoli impurità o particelle sospese, ma anche in altre situazioni in cui li liquido a contatto diretto con il sensore potrebbe causare danni o problemi di misura.
A seconda del fluido del quale andrà misurata la pressione, varierà il materiale di cui è composto il separatore:
PVC: per acidi, alcali, detergenti, alcool, olio, grassi, benzina, idrocarburi alifatici, acqua;
PP: per acidi organici e inorganici (quasi tutti), basi, sali, anche a concentrazioni elevate
PVDF: per acidi organici e inorganici (quasi tutti), soluzioni saline e solventi
Nelle varie applicazioni i manometri vengono inseriti nel punto in cui si vuole rilevare la pressione statica, e più precisamente la pressione relativa (calcolata cioè rispetto all’ambiente). Nell’immagine che segue si possono vedere alcuni esempi di possibili installazioni.
-
Separatore in PVC, PP o PVDF -
Manometri standard -
Manometro in acciaio con o senza glicerina
La misura della pressione e pompe centrifughe
La misura della pressione, così come di altre variabili quali la temperatura, è fondamentale per monitorare il comportamento di una pompa: attraverso questi valori è possibile rilevare tempestivamente guasti o malfunzionamenti e rendere quindi molto più sicuro il funzionamento dell’impianto.
Per mantenere una certa precisione durante la misurazione della pressione e della velocità del fluido, in corrispondenza dei punti di misura non ci devono essere elementi di disturbo. Tutti gli organi installati nelle tubazioni, che possono influire su un flusso del liquido lineare, parallelo e privo di vortici, devono essere considerati elementi di disturbo, dunque bisogna valutare il punto opportuno (vedi figura, parte destra).
In generale, il manometro deve essere installato in modo da evitare l’esposizione a fonti di calore, vibrazioni e per ottenere una facile lettura del valore sul quadrante.
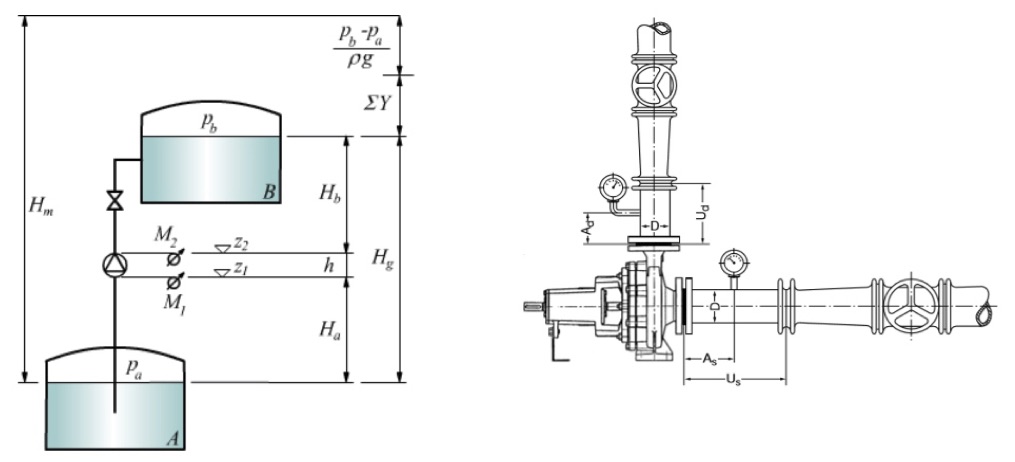
È uso comune installare il manometro completo di valvole di intercettazione per facilitare la sostituzione mentre il sistema è pressurizzato e per escludere il manometro quando la lettura non è richiesta. La misura della pressione definisce anche alcuni importanti grandezze fisiche di un impianto di sollevamento, in cui una pompa centrifuga collega due serbatoi (cfr. figura parte sinistra).
Si definisce prevalenza geodedica Hg la differenza di quota tra la superficie libera del liquido contenuto nel serbatoio A e la superficie libera del liquido contenuta nel serbatoio B.
Un parametro caratteristico delle pompe è la prevalenza manometrica Hm definita come la variazione di carico misurato con un manometro M2 posto tra la bocca di mandata e quella di aspirazione della pompa in cui è situato un altro manometro M1 (vedi figura).
La prevalenza manometrica può anche essere definita come l’energia necessaria che la pompa deve conferire al fluido per mandarlo dal serbatoio A al serbatoio B.
In alcune applicazioni può essere utile impiegare sensori compatti, come la serie PTM, funzionamento a secco e per il controllo delle pompe in plastica, contenente un sensore di pressione e di temperatura concepito per la protezione da funzionamento a secco e per il controllo delle pompe in plastica, contenente un sensore di pressione e di temperatura (vedi figura seguente).
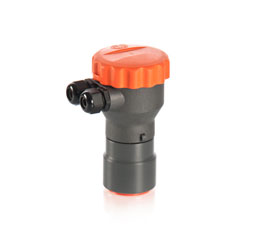
Questo sensore (nella versione a relè, con 4 uscite programmabili) può essere utilizzato anche per lo spegnimento automatico della pompa, limitando così i tempi di inattività e i costi che ne derivano.
Nella figura seguente è rappresentato un esempio in cui sono evidenziati i range di temperatura e pressione (fino a 10 bar) a seconda del materiale impiegato (PP, PVDF o PVC).
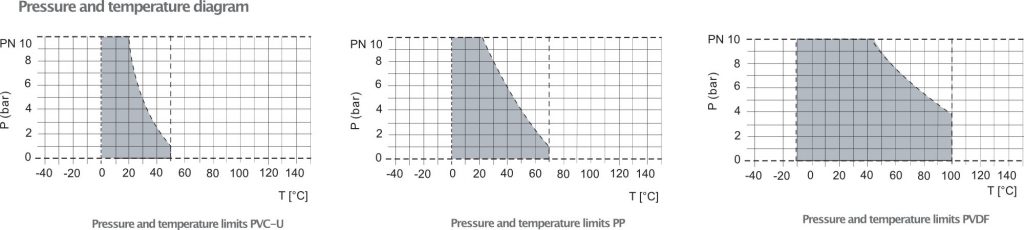
FONTI www.edutecnica.it
Scrivi un commento