di Michele Cifalinò
La scelta delle valvole negli impianti industriali è un tema importante: la funzione delle valvole, infatti, è fondamentale, sia per ragioni funzionali (regolazione o intercettazione del fluido nelle tubazioni), sia per ragioni di sicurezza.
Esistono diversi criteri di classificazione a seconda della funzione o in base al principio di regolazione: un primo criterio è evidenziato nell’immagine sottostante.
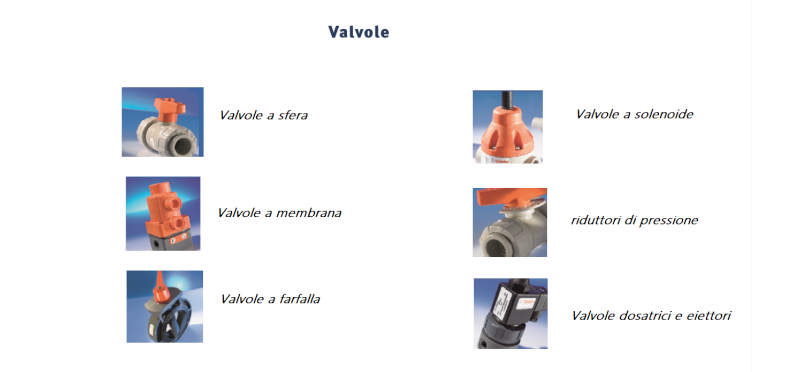
A seconda poi della funzione che assolvono in un impianto, le valvole possono suddividersi in :
• valvole di intercettazione e regolazione
• valvole di ritegno
• valvole di sicurezza
Valvole di intercettazione e regolazione
Le valvole d’intercettazione hanno la funzione di isolare una parte dell’impianto con lo scopo di consentire operazioni di manutenzione o sostituzione di parti senza che l’impianto stesso debba essere completamente svuotato; vengono disposte in diversi punti delle tubazioni e hanno la caratteristica di poter funzionare o completamente aperte (con le minime perdite di carico possibile) o completamente chiuse (durante la manutenzione dell’impianto).
Le valvole di regolazione consentono di variare la portata erogata dalla pompa mediante un organo otturatore, che può assumere diverse posizioni imposte dall’esterno mediante comandi manuali o automatici. Solitamente questa tipologia di valvole è sempre inserita nel tratto di mandata della tubazione onde evitare il pericolo d’innesco della cavitazione.
Valvole di ritegno
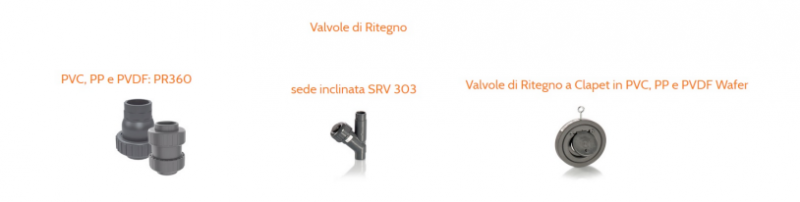
Hanno la funzione d’impedire lo svuotamento dell’impianto in caso d’arresto della pompa. Sono dotate di un elemento mobile (sfera, saracinesca, ecc…) che si apre durante il moto del fluido in una direzione e si chiude automaticamente quando il fluido tende a fluire in senso opposto (per tale ragione sono dette anche unidirezionali). Possono essere disposte orizzontalmente o verticalmente e la loro chiusura può essere provocata da una molla di richiamo o dall’azione fluidodinamica del liquido oppure possono essere inserite in posizioni intermedie a protezione della pompa o di altre parti dell’impianto da eventuali colpi d’ariete.
Valvole di controllo/sicurezza
Le valvole di controllo hanno lo scopo di mantenere la pressione nell’impianto entro valori prefissati, mentre quelle di sicurezza hanno la funzione di proteggere l’impianto, o parti d’esso, da pericolose sovra pressioni dovute a errori di manovra o a mal funzionamento dello stesso.
Criteri di scelta di una valvola in un impianto: alcuni esempi
Vediamo ora alcuni criteri, seppur generali, per selezionare una valvola specifica per una certa applicazione. Prima di tutto nella scelta del tipo di valvola da impiegare occorre certamente valutare diversi fattori, fra cui:
• il materiale della valvola
• la caratteristiche del fluido: presenza di particelle sospese, corrosività, ecc..
• la portata massima di esercizio ed il campo di regolazione di portata;
• la caratteristica di portata.
• Il tipo di controllo (manuale o automatico).
La scelta del materiale, ad esempio, si stabilisce in base alla concentrazione chimica e alla temperatura del fluido: spesso sono necessarie applicazioni con fluidi aggressivi, ad alte pressioni e ad alte temperature, è il motivo per cui in diverse applicazioni nell’industria chimica si impiegano il PVC, PP, PP-n, PE, PVDF, PTFE.
Un tipo di valvola di regolazione molto diffusa è la valvola a sfera, nella quale la tenuta del fluido è realizzata da una parte sferica che ruota all’interno del corpo.
Se il diametro del foro di passaggio è lo stesso del tubo a cui è la valvola è collegata, si parla di valvola a passaggio pieno: la posizione chiusa questo tipo di valvola garantisce una buona tenuta stagna. Per il loro costo relativamente basso, queste valvole sono utilizzate con successo in molte applicazioni, anche se spesso non consentono una regolazione particolarmente precisa.
Esistono anche valvole a sfera appositamente studiate che, grazie alla sfera interna sagomata, consentono una regolazione molto più precisa rispetto alle valvole tradizionali, grazie anche all’indice graduato posto sulla leva a segnalare il grado di apertura. (ad esempio serie speciali come la C200 PROP oppure la C200 DOS, come mostrato nella figura seguente)
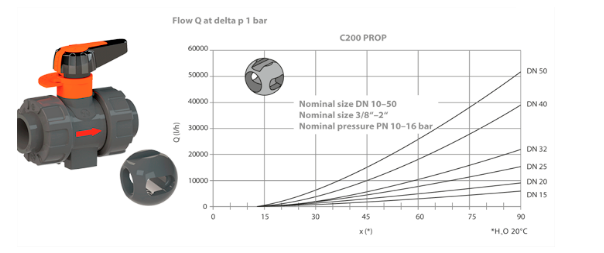
In altre applicazioni, per la regolazione del flusso sono privilegiate le valvole a membrana: queste valvole hanno spesso una limitata capacità di variare l’apertura per regolare la portata e sono particolarmente indicate per sostanze corrosive, fanghi leggeri, fluidi viscosi, sospensioni solide.
In generale, quando è richiesta un’alta frequenza di apertura e chiusura unitamente all’esigenza di movimentare liquidi con parti solide in circolazione, sono indicate le valvole a membrana. Per alcune applicazioni speciali esistono anche valvole munite di “doppia membrana” che consente di lavorare con pressioni nettamente inferiori a quelle necessarie alle valvole a pistone: questa caratteristica è ideale quando non si ha la certezza di avere una pressione elevata costante. Se da un lato la tenuta stagna di queste valvole è eccellente, perché fluido e asta non entrano in contatto diretto, dall’altro possono essere rilevanti i costi di manutenzione.
Come nel caso delle altre valvole, la regolazione può essere sia manuale che automatica.
Di seguito una panoramica dei modelli più utilizzati per questo tipo di valvole.
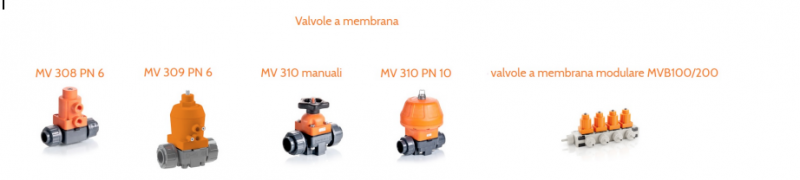
Infine in altre situazioni, soprattutto quando l’impianto tratta grandi volumi di liquido che devono essere gestiti nella massima sicurezza (come nell’industria chimica e nell’industria pesante, così come nei grossi impianti industriali e nella tecnologia ambientale) si possono impiegare valvole a farfalla, in cui l’otturatore è un disco che ruota attorno ad un asse perpendicolare a quello del tubo, ostruendo il passaggio. Le valvole a farfalla garantiscono peraltro una buona tenuta stagna; i modelli di grande diametro generalmente si caratterizzano per un montaggio a flangia, ma alcuni modelli vengono montati tramite avvitamento. Le valvole a farfalla, nella maggior parte dei casi, si distinguono per un ingombro minimo, soprattutto rispetto alle valvole a sfera.
Anche le così dette valvole di fine linea a farfalla in PVC, PP e PVDF sono particolarmente utili per velocizzare le operazioni di riempimento e svuotamento dei serbatoi e se installate alla fine di una linea permettono di collegare agevolmente i tubi flessibili impiegati per trasferire i liquidi.
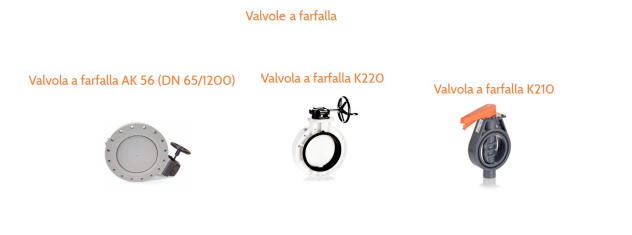
Un’applicazione: i sistemi di innesco e di scarico
In questo esempio relativo all’impiego delle valvole, vediamo alcuni sistemi ausiliari che hanno la funzione di consentire il riempimento e lo svuotamento dell’impianto. Il sistema d’innesco è necessario quando una pompa non auto-adescante non è posta sotto battente poiché da sola non è in grado di produrre una depressione sufficiente ad aspirare il liquido dal serbatoio d’aspirazione. In tal caso è necessario riempire di liquido la pompa e tutto il tratto d’aspirazione: è opportuno osservare che, in ogni caso, l’azionamento di una pompa non innescata è da evitarsi a causa di possibili danneggiamenti che possono essere provocati dallo strisciamento di parti metalliche in moto relativo e a contatto diretto.
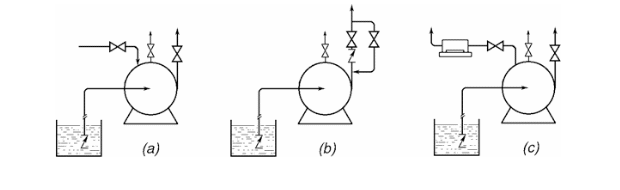
Nella figura sono rappresentati alcuni sistemi d’innesco, vediamoli nel dettaglio:
• a) la pompa è dotata di una tubazione d’alimentazione, dalla rete idrica o da un serbatoio ausiliario, che consente l’innesco.
• b) nell’impianto è presente una derivazione sul tratto di mandata che scavalca la valvola d’intercettazione; essendo il serbatoio di mandata posto più in alto della pompa, questa verrà riempita aprendo la valvola posta sulla derivazione. Nel caso in cui il serbatoio di mandata sia allo stesso livello della pompa, oppure al di sotto di essa, la derivazione dovrà essere collegata ad un serbatoio ausiliario posto al di sopra della pompa.
• c) la pompa è collegata ad una pompa a vuoto per l’aspirazione dell’aria.
Dall’esame della figura, si evince che l’impianto è dotato di valvole di spurgo che permettono la fuoriuscita dell’aria durante la fase d’innesco della pompa; tali valvole sono generalmente collocate sopra la pompa e in corrispondenza dei punti dell’impianto dove si possono formare sacche d’aria. Per quanto riguarda lo scarico dell’impianto, esso è realizzato mediante valvole di spurgo poste nei punti più bassi dell’impianto e con un’opportuna canalizzazione che consenta lo scarico del liquido.
FONTI:
Prof. Camuzzo “Dispense di automazione industriale” – Politecnico di Milano
Scrivi un commento