di Chiara Landolina
L’ottimizzazione CFD degli impianti (Computational Fluid Dynamics) permette di migliorarne il rendimento a partire da un’analisi accurata delle formule che descrivono il comportamento dei fluidi coinvolti nei processi.
I fluidi vengono movimentati e trasportati da una sezione dell’impianto all’altra dalle pompe. La portata che erogano dipende dalla pressione di mandata, dalla tipologia di macchina, dal numero di giri e dalle resistenze incontrate dal fluido lungo il percorso.
Classificazione delle pompe
A seconda di come viene trasferita l’energia al fluido possiamo classificare le pompe in due categorie: pompe volumetriche e pompe cinetiche. In queste ultime, grazie all’azione di forze centrifughe, il liquido incrementa dapprima la sua energia cinetica e successivamente avviene la trasformazione in energia di pressione. A questa categoria appartengono le pompe centrifughe, largamente utilizzate, e le pompe assiali.
Nelle pompe volumetriche, invece, il liquido viene spinto dall’organo in movimento che fa tenuta con la carcassa e l’energia viene trasferita al liquido aumentandone direttamente la pressione. A questa categoria appartengono la pompe alternative e rotative.
Le pompe volumetriche sono caratterizzate da elevate prevalenze e portate medio-basse, possono essere utilizzate per liquidi a bassa e alta viscosità, mentre nel caso di solidi sospesi, fanghi e solidi filamentosi è meglio evitarne l’impiego perché i solidi potrebbero bloccare le valvole di aspirazione e mandata o ridurre significativamente il rendimento volumetrico e meccanico della macchina.
Gli svantaggi principali delle pompe alternative sono gli elevati costi di investimento e la portata erogata non continua; queste caratteristiche le rendono inadatte ad alcuni processi e applicazioni.
Di contro, le pompe cinetiche sono caratterizzate da elevate portate (medie nelle pompe centrifughe e alte nelle pompe assiali) e, a seconda del numero di stadi, possono garantire prevalenze medio-alte. Le turbo pompe di ultima generazione trattano efficacemente fanghi e solidi sospesi filamentosi (giranti aperte) ma non sono comunque adatte a processare liquidi viscosi.
Efficienza delle pompe
La prevalenza teorica di una pompa è il rapporto fra la variazione di pressione che subisce il fluido durante il passaggio nella macchina e la sua densità moltiplicata per l’accelerazione di gravità :
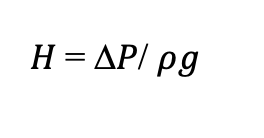
La potenza teorica fornita al fluido, PT [W] è definita dalla seguente equazione:

dove ?̇ [m3/s] è la portata volumetrica di fluido erogata dalla macchina.
La potenza realmente assorbita all’albero del motore accoppiato alla macchina, Pa [W] è invece funzione del rendimento della pompa (che varia usualmente nell’intervallo 0.6-0.85):
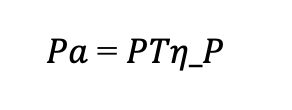
Il rendimento della pompa è dato a sua volta dal prodotto di 3 rendimenti:
- Rendimento meccanico, funzione dell’attrito fra la parte rotorica e statorica della macchina, principalmente albero e cuscinetti
- Rendimento volumetrico, funzione dei trafilamenti di portata utile e quindi delle perdite di fluido nei giochi interni, dovuti anche a causa della presenza di gas
- Rendimento idraulico, funzione delle perdite di carico nella pompa.
In linea teorica è possibile incrementare ognuno di questi rendimenti, ma generalmente quello che più influenza il prodotto finale è il rendimento idraulico, che risulta massimizzato nel momento in cui
vengono rispettati i seguenti aforismi:
- ingresso del fluido nella zona rotorica senza urti (quindi velocità di uscita tangente al profilo delle palette, aforismo rispettato sia nel caso di profilo delle pale rivolto in avanti e in indietro)
- uscita del fluido dalla zona rotorica alla minima velocità (aforismo rispettato solo nel caso di profilo delle pale rivolto all’indietro). Questo implica che, a parità di condizioni, la sola scelta del profilo della palettatura della girante influenza il rendimento della macchina.
Accoppiamento pompa-impianto
Una volta scelto il tipo di pompa essa va inserita nell’impianto identificando il punto di funzionamento. Per fare ciò è necessario tracciare, oltre alla curva caratteristica della macchina, la curva caratteristica del circuito o dell’impianto.
La curva del circuito dipende dalla prevalenza statica e da quella dinamica, la prima è indipendente dalle condizioni fluido-dinamiche (indipendente da Re) e è funzione della differenza di quota fra il pelo libero del liquido in aspirazione (da un serbatoio, da un’apparecchiatura generica, o nel caso di pompa sommersa, dal pelo libero sopra la macchina) e della differenza delle pressioni nella zona di aspirazione e in quella di mandata; mentre la parte dinamica è funzione delle altezze cinetiche e delle perdite di carico incontrate lungo tutto la linea, dalla zona di aspirazione a quella di mandata.
Il contributo delle perdite di carico è particolarmente importante ed è dato dalla somma delle perdite di carico localizzate Yd [m], quindi dovute alla presenza di elementi quali valvole, polmoni, gomiti, variazioni di sezione ecc. (quindi dovute al distacco della vena fluida principalmente), e delle perdite di carico continue lungo le tubazioni Yc [m], dovute alle perdite energetiche per le forze di attrito fra il fluido e le pareti interne delle tubazioni.
Scrivi un commento