di Chiara Landolina
Un settore in forte espansione è quello che si occupa della produzione di disinfettanti e detergenti. Vediamo come sono composte queste sostanze e quali caratteristiche devono avere gli impianti per la produzione di tensioattivi.
Composizione e produzione dei tensioattivi
Il componente principale di un detergente è il tensioattivo: un materiale la cui molecola è composta da una “coda” idrofoba e da una “testa” idrofila. Essi sono in grado di abbassare la tensione superficiale di un liquido agevolando la bagnabilità delle superfici e la miscibilità tra liquidi diversi. La loro funzione nei detergenti è quella di emulsionare lo sporco e quindi di rimuoverlo grazie alla loro capacità di diminuire le forze (tensioni superficiali) che tengono lo “sporco” attaccato alle superfici.
I tensioattivi si dividono in quattro classi:
- Tensioattivi non ionici: sono alcoli a lunga catena, come i derivati poliossietilenici degli acidi grassi o gli APG (alchil-poli-glucosidi)
- Tensioattivi anionici: in genere sono sali costituiti da lunghe catene di atomi di carbonio erminanti con un gruppo carbossilato o solfonato. Alcuni esempi sono: il sodio lauril solfato (SLS), il lauril etossi solfato (LES), numerosi acidi alchil-benzen-solfonici (ABS).
- Tensioattivi cationici: Sono sali di cui è importante la parte positiva, costituita da lunghe catene di atomi di carbonio terminanti con un gruppo ammonico quaternario. Hanno un buon potere disinfettante ma basso potere detergente. Il BAC (benzalconio cloruro) è uno dei più utilizzati nei detergenti, avendo anche proprietà germicide. Altro esempio è il bromuro di cetil-trimetilammonio (CTAB) o bromuro di esadeciltrimetilammonio.
- Tensioattivi anfoteri: si comportano come tensioattivi cationici in ambiente acido o anionici in ambiente alcalino. Alcuni esempi sono la cocco-ammidopropil-betaina, la dodecil-betaina, la lecitina e gli acidi amminocarbossilici.
Gli altri componenti di cui è composto un detergente sono:
- sequestranti per addolcire l’acqua.
- candeggianti (ad esempio ipoclorito perborato di sodio, acqua ossigenata) per sbiancare.
- enzimi per decomporre lo sporco formato da proteine, grassi o carboidrati.
- solventi come etanolo, isopropanolo o ammoniaca.
- altri componenti per il controllo della schiumosità, profumi, coloranti, azzurranti ottici, emulsionanti, addensanti.
Fasi del processo di produzione di un detergente
Il processo di produzione di un detergente è piuttosto complesso, come è possibile notare dallo schema di un impianto per la produzione che segue.
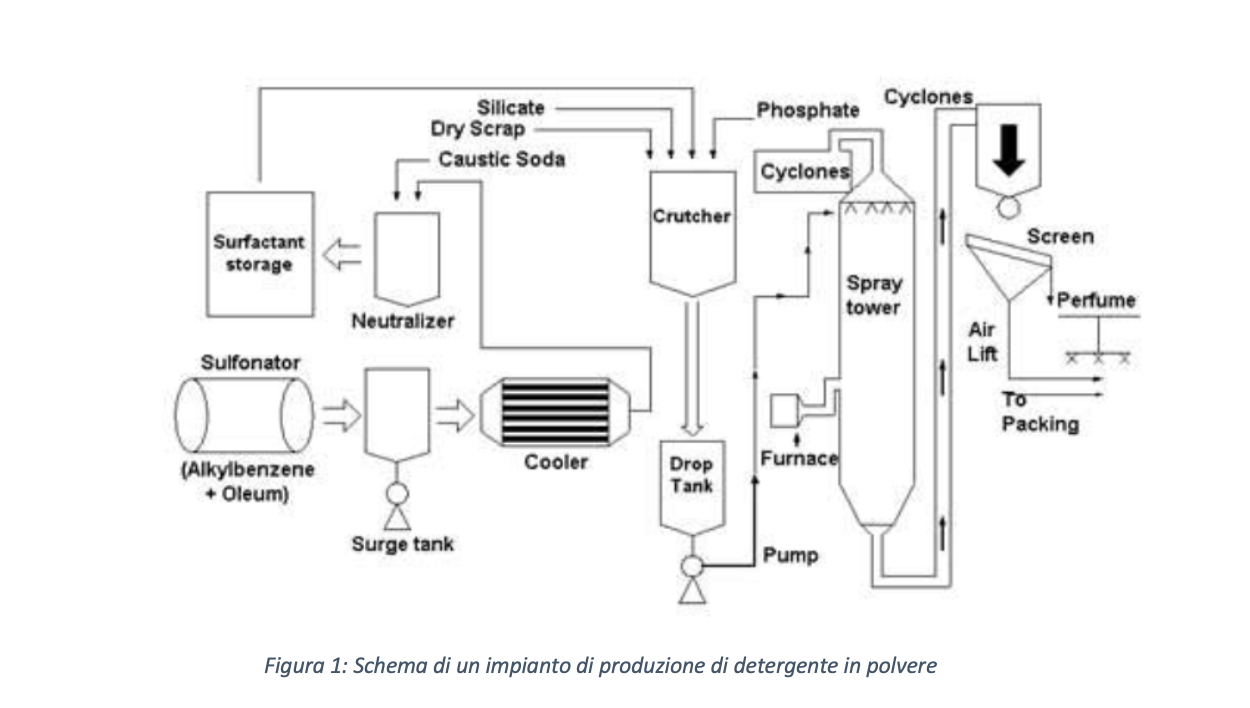
- Produzione del tensioattivo grazie ai processi di solfonazione, solfatazione (le cui reazioni sono visibili in figura 2 e 3) e neutralizzazione.
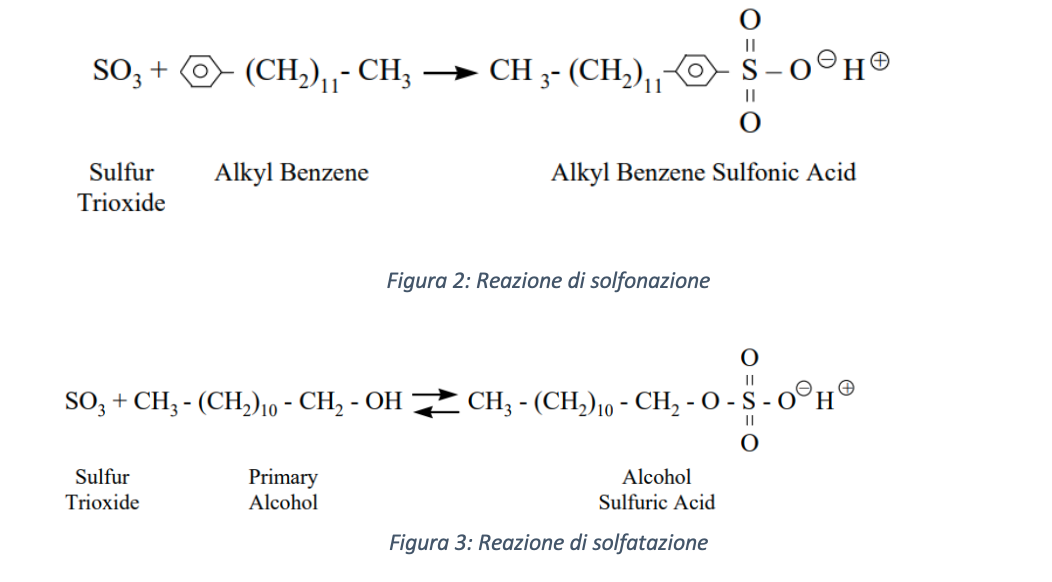
2. Una volta prodotto il tensioattivo, esso viene stoccato e successivamente viene inviato al miscelatore dove avviene la miscelazione ad alta temperatura con gli altri ingredienti: acqua, profumi, soda caustica, acido solfonico, tripolifosfato di sodio.
3. La terza fase consiste nel raffreddamento della miscela e nell’aggiunta degli enzimi in forma di polvere. Gli enzimi hanno la funzione di aiutare la rimozione delle macchie.
Pompe per la produzione di disinfettanti e detergenti
Per poter movimentare le materie prime, le miscele semilavorate e il prodotto finito sono necessarie pompe che abbiano come caratteristica principale la capacità di non rovinarsi a contatto con sostanze aggressive. Ad esempio soluzioni con una percentuale elevata di soda caustica, liquidi contenti ammoniaca, candeggina e molte altre sostanze usate nella produzione dei detergenti, a causa del loro potere corrosivo, non possono entrare a contatto con i metalli. In questi casi è necessario scegliere materie plastiche come il PVC/PVDF, che sono più resistenti.
Un’altra criticità legata ai liquidi usati in questo settore riguarda l’elevata viscosità e la presenza di granuli che spesso li caratterizza. Anche queste condizioni portano ad una rapida usura delle pompe.
Sicuramente il primo componente che si usura in una pompa per applicazioni chimiche è la tenuta meccanica.
La frequenza con la quale tenuta meccanica, guarnizioni e componenti interni vanno sostituiti dipende da:
- Composizione chimica del fluido
- Corrosività
- Viscosità
- Temperatura
- Presenza di particelle solide
- Punto di funzionamento della pompa (più è vicino al BEP meglio è)
La scelta di una pompa non adatta alla nostra applicazione, oltre ad avere gravi ripercussioni sulla sicurezza degli impianti, ha importanti conseguenze anche dal punto di vista economico. Infatti gli interventi di manutenzione ordinaria e straordinaria (dovuti alla sostituzione di componenti usurati) saranno più frequenti ed invasivi e porteranno a fermi impianto con evidenti ripercussioni economiche.
Scrivi un commento